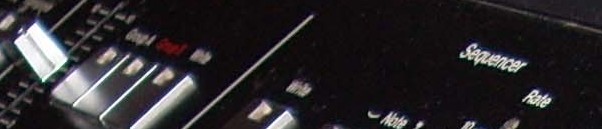
Move your Body... Shake your Soul !
DIY ACOUSTIC PANEL (THE HARD WAY) Text Only
STEP 1 FRAME
Make your carpenter cut the pieces at your favourite measures. In my case those measures are: 2 200 cm long pieces, and 3 pieces 120 cm long, all with a width of 11 cm. The wood is 16 mm thick agglomerated wood. The cheaper I found. DM is more expensive and wheights more. 6 metal squares add rigidity and 32 screws, stability. Besides some wood squares, from a single strip of wood. Pictures self explain. ¡C`mon get dirty!
The little box you see, in the bottom side of the frame, is a pug box to have access to the power sockets I have in the wall. If you ever have to build a panel like this, lift the structure to the desired position, and mark on the lower listel, the position of the plug box in relation to wall sockets. After, screw the power box to the lower listel. It’s a bit complicated I know, but ¡this is the hard way!.
STEP 2 HUNGING SYSTEM.
A detail not to miss: On the wall side of the frame I stappled provisionally some pieces of cloth, over those I nailed little DM pieces, of the same quality as those that will form the rear panel enclosure. All of that to have a reference about the distance to maintain from the wall, THE TIME TO MARK THE POINTS WHERE TO DRILL THE HOLES IN THE FRAME. Once marked those points, drills can be made. And once drills are made, you can remove those reference pieces.
Here is the invisible hunging system schematic. After marking with pencil on the wall, the position of top frame, drill on the wall two holes at 31 mm from upper frame downside. In these holes you will place two rings like shown in the picture. It has a 10 mm inner hole perfect for the 8 cm long metric screws we have.
To mark the points where to drill the holes in the frame, for the metric screws, proceed as shown in the picture. Glue the marker with fast white glue. I used Ponal express.
More detailed picture about the proceeding. At this phase the frame wheights between 10 and 15 kg.
Once made the drills, bring the frame, put it upside, and in the upper frame stapple the cloth, on the back side of the frame. Once stappled, find the drill holes, softly make holes on the cloth, and place the screws with their washers and female screws. Once made this, roll the cloth so it don’t occupy more than upper frame width. Fix it with strips of carton and isolating tape .¿isn’t it simple?. That’s the hard way!
Now comes the CRITICAL STEP: Once placed the screws and its female crews, as shown in the pictures, 1. hung the frame on the wall hunging points. 2. Adjust the frame level with the lower female crews until its completely horizontal.3. Once everything is levelled, FIX THE LOWER SCREWS WITH GLUE. 4. once the glue is dry, unhung carefully all the frame from the wall, in order to continue with the next step. ¡those muscles!.
STEP 3 (OPTIONAL) FRONT PAPER
This step is optional. If you bought Rock Wool, this comes with two faces of protective paper. I put plates of glass fibre, and to avoid to breath the little particles, I put the sheet of paper in the front side of the frame. If you try to glue this paper, make it with liquid white glue. Avoid Stick glue, is for children.
STEP 4 CLOTHING
Difficult phase where available. Is so difficult I can’t remember how I did it.
Place the frame over four carpenter horse. Extend the cloth over the frame. Locate the power box and mark an X where you will make the cut. The first piece of cloth to glue, is the one from the upper side of the power box. At this stage a wrinkle is nearly inevitable. I hope you are lucky. Use a special cloth glue, like textile Ceys. Glue the four inside sides carefully and let dry 24 hours. Do another thing in the meanwhile: A new track, take a walk, Have a sunbath, etc..
Once glue is dry, you can start tauten the cloth so it gets smooth. Method: Tense and Staple, tense and staple,…. Till you finish. And all without moving the frame from its place, always in horizontal position. In some moments you will have to move the carpenter horses, to work comfortably. In between each staple let some 3 or 5 cm, because later you will have to nail the rear panel to the frame. Attention!! Staplers make a lot of noise, protect your ears with ear taps. ¡Courage! Tense and staple, tense and staple, tense and staple, tense and staple….
With the frame lay down on the ground, apply double cloth layer for the power box. In between these two layers place kraft paper in order to protect the upper layer from glue. The remaining work is to be handy and have patience. Only to give this finish It took me 2 hours.
Folding detail on the squares. Very professional.
STEP 5 FIBRE
Cut and place. Oversize 1 cm approximately so the fibre gets engaged under the frame pressure. Watch out the borders don’t underlay too much. I placed two layers of fibre, because I thought 3 would be too much bulky. Let 10 cm in excess of cloth to cover the fiber.
Use a ventilated mask and good scissors. Place the frame panel, aver a plastic to protect the cloth from ground dirt. Her I realize the cloth thikness in the squares was the double than I planned. You may have to staple and distaple, to remove a cloth layer and make it thinner. That difference luckily is not critical for a good hung of the system, I mean…
panel.
STEP 6 REAR PANEL
Another CRITICAL PHASE. Pay attention to the play. 1. Once filled the panel with fiber, fix the rear panels with 8 nails. 2. lift the entire panel. 3. mark with a pencil the outline of the power box. 4. lay the panel on the ground, remove the 8 nails, and cut the outline you marked with the pencil. Pay attention to the pictures. Like Eagle owls .
An IMPORTANT DETAIL: In the lower frame a did a 1cm depth notch to let pass the wires. In that point cloth is less tense, and will mold itself to wires thikness. Also its necessary to cut a little DM section, to let pass those wires.
Before nailing the rear panels, mark with pencil the position of every nail, in between each staple. I think I used as many as 150 nails.
Concerning screw hole, the most important detail, is that you let 2cm from the end of screw up to the fibre. Because at the hunging , the fixing rings on the wall can pass and fit below panel screws. ¡Be lucky!
STEP 7 WEIGHT
At this point, the finished panel wheights 25 kg.
¿Did you go to gym? ¿No?, ¡Start training hard!
If you have build the panel in a different room from which is to be its final place, drag it over a blanket, up to place P, at hour H. because when moment M arrive, that will be very important.
STEP 8 PLACING THE PANEL
Moment M has arrived. Let’s suppose you went to gym, you trained hard and now your hands don’t get sweaty. We are right.
To hung the panel I did it in 4 steps.
- Separate the rack cabinet from wall. I had to disconnect a lot of wires.
2. Place the panel over the cabinet you see in picture.
- By freehand, lift it up to the wall anchorages.
3.1 It didn’t enter at first attempt, but it stood there maybe leaning the two screws ¡¡over the border of the two rings!!.
- Terminate, pushing and catching by below softly, up you notice that the two screws enter the rings. A really difficult moment. ¡May the force be with you!
For security, although the panel stands with only the two anchorages, I put a 60 by 60 mm steel L below the panel, once hung. Mark 3 holes with pencil, put three 6 mm plugs and screw. The most difficult hole is the nearest to the panel. You may have a little roominess, fill it with a piece of plastic or metal, undersized to L perimeter.
And the result is what you see in the picture.
Spectacular but not easy at all. Anyway, ¡this is the hard way!
AZEL909